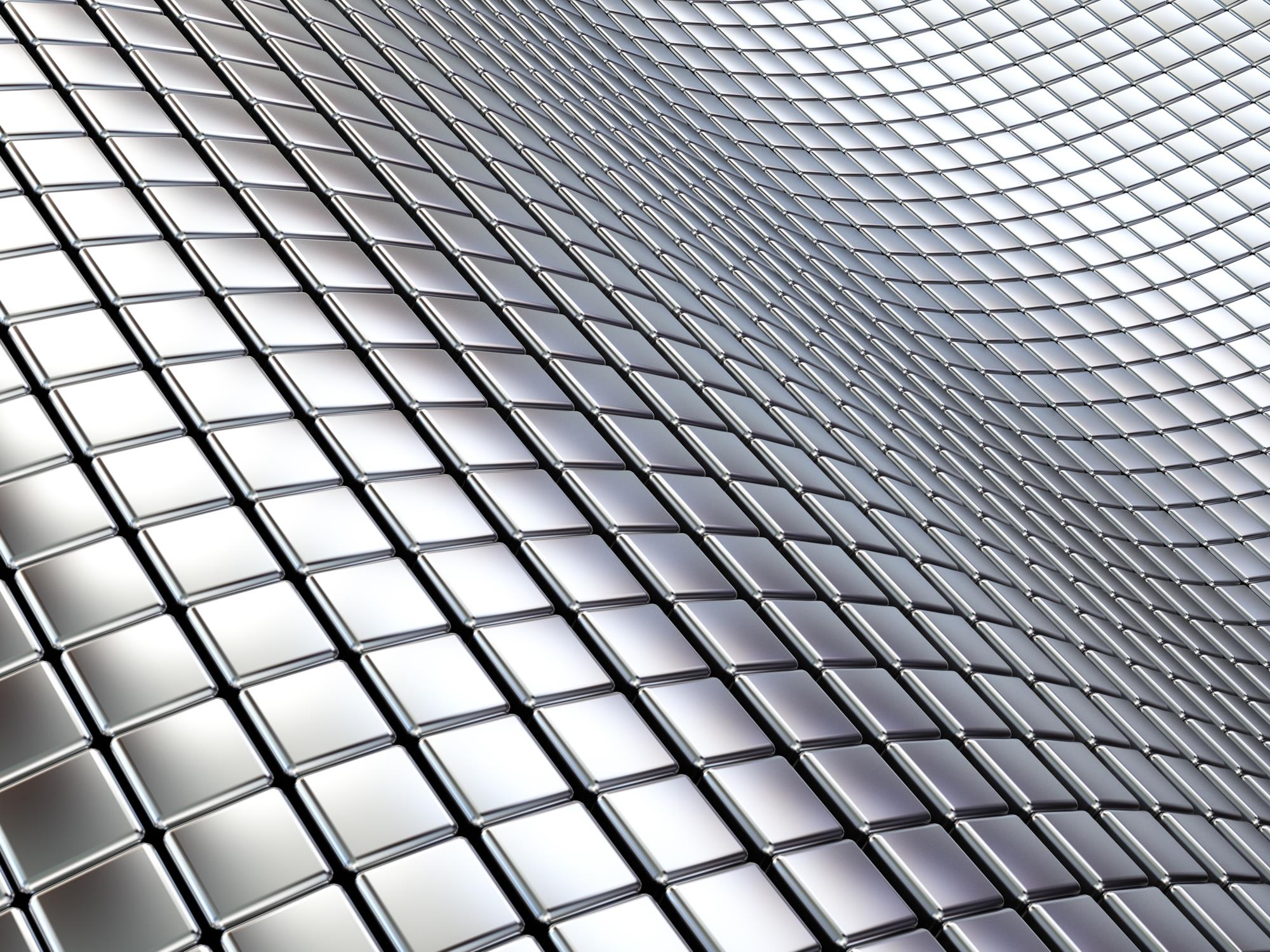
Can stainless steel rust?
Can stainless steel rust?
The term “stainless steel” often misleads us and so we mistakenly believe that stainless steel products are not affected by the problem of corrosion under any circumstances and at any time.
In the following text we will now analyse if, when and why stainless steel can corrode and what kind of measures could prevent this.
Does stainless steel rust?
First of all, stainless steel can also rust. However, stainless steels are very robust and highly resistant to corrosion under regular conditions because they contain, among other things, chromium.
If this element is present in sufficient quantities in the alloy and if it is exposed to the oxidative effects of acids, alkalis, water, air and other media, a very thin (130 Angstroms), impermeable layer of chromium oxide (CrO) forms on stainless steels, which prevents corrosion and keeps the material rust-free, unlike regular mild or carbon steel.
These proportions of chromium must be evenly distributed in the chemical composition of the material to give it the resistance of stainless steel. Corrosion (rust) thus forms on stainless steel surfaces when they are exposed to an aggressive load and there is not enough chromium to create and maintain the necessary oxide layer.
When does stainless steel rust?
Many cases of rust on the surface of stainless steel are caused by damage to the protective layer of chromium oxide.
During the processing of the material or the production of stainless steel products, damage to the protective layer is very often caused by thermal and/or mechanical stress (e.g. welding and grinding). Therefore, “freshly treated” surfaces can be particularly susceptible to corrosion and careful reworking and maintenance of these areas is necessary.
Another circumstance in which rust can occur on stainless steel is possible contact with conventional carbon steel or low-alloy steel. When working with stainless steel materials and products, it is important to ensure that they do not come into contact with any ordinary steel.
For example, when working in the construction industry, strict care must be taken to ensure that no particles of the construction steel (for instance when cutting reinforcements) come into contact with stainless steel surfaces (for example the one of façade elements). These can stick to the stainless surface, which then leads to small sources of corrosion in form of specks or small spots.
Such contact corrosion can be removed with agents specially designed for cleaning such contamination on stainless steel. However, this can lead to visual changes or optical impairments on certain aesthetic surfaces.
Damage to the protective layer and subsequent contamination is also possible during processing and fabricating, if steel tools or “conterminated” uncleaned stainless steel tools or other objects come into contact with the surface of the stainless steel.
In addition to the factors mentioned above, contamination during or after processing respectively during or after installation is one of the main factors for corrosion.
If the surface is never cleaned, cleaned too infrequently or not cleaned properly, rust can also form underneath longer termed dirt that has not been removed. Therefore, it is always advisable to check the stainless steel surfaces thoroughly after processing or working and to clean them if necessary, or to maintain them regularly and properly during their life cycle if circumstances make this necessary.
Can rust on stainless steel be prevented?
However, the above points should not change the fact that stainless steel is a very robust, extremely uncomplicated and “rewarding” material.
If you observe certain rules and measures when storing, transporting, handling, processing, installing and maintaining stainless steel products, then in principle most of the factors that cause rust to form on stainless steel can be avoided.
Store and process the stainless steel materials and products in premises that are protected from the effects of weather, dust, dirt and the like. If, on the other hand, the stainless steel materials or products are stored or processed outdoors, there is a risk that water (including condensation due to temperature fluctuations), dust or dirt will cause reactions on the metal surfaces.
During storage and processing, they must not come into contact with items made of other materials that do not have anti-corrosion properties. The interaction of materials with different compositions can lead to chemical reactions and the formation of rust.
When manufacturing or installing products such as stainless steel façade elements, use only suitable and cleaned tools. Avoid the simultaneous use of materials, tools, equipment or other aids made of stainless steel and conventional steel or iron, as well as those of tools that have not been thoroughly cleaned of impurities or are rusty.
During transport, protect stainless steel with paper interleaves, protective PVC films or other packing materials, and it should also not come into contact with nails of wooden pallets or with tension straps made from mild steel.
Do not store or ship sheets or parts made of different steel alloys together in one package.
Rust protection can also be extremely improved by a specific choice in the various surface treatment finishes that are possible with stainless steel.
For example, mirrorINOX offers to provide the stainless steel surfaces with the processing method “nanoINOX® coating with anti-fingerprint and easy-to-clean properties”.
This not only makes the surfaces extremely attractive, but also reduces dirt adhesion, supports a self-cleaning effect and makes the surfaces much easier to clean and maintain.
How can rust be removed from stainless steel?
If the stainless steel is now affected by corrosion, there are still methods and means to remove the rust from the surface of the materials.
In this way, the functionality of the surface can be restored or maintained.
However, as mentioned above, care must be taken to ensure that the cleaning does not cause any optical damage or impairment such as scratches, change or loss of colour to the finishes used in optical applications.
Corrosion can be removed chemically using rust converters. For the cleaning and subsequent care of stainless steel products, only use cleaning agents that have been specially developed and approved for exactly this purpose.
After cleaning, rinse the product with as much, ideally distilled, clear water as possible and dry the surface with compressed air or a soft cloth that is not abrasive under any circumstances.
Cleaning, care and disinfecting agents containing chlorine, solid abrasives (abrasives), acids or alkalis should not be used, as all these substances can attack and destroy the protective oxide layer.
In the worst case of very severe corrosion, the surface of the stainless steel products can be treated by blasting, grinding or polishing. In any case, an expert should be consulted and the procedure should be discussed and clarified with him.
Why is it important that stainless steel does not rust?
Keeping the surfaces of stainless steel products and applications in perfect condition is not only a question of aesthetic appearance.
Severe, deeper corrosion can seriously impair functionality (see pitting corrosion, perforation, stress corrosion cracking, vibration corrosion cracking, crevice corrosion) and negatively change the mechanical properties of the material, making it more brittle, for example.
Some stainless steel corrode more easily. Others do not.
Where stainless steel is used:
The main alloying element in stainless steel is chromium (the proportion in the alloy is 12-20 %). To improve corrosion resistance, nickel, titanium and molybdenum are also added to the alloy in varying amounts, depending on the properties required. To keep it simple, we will look at the most common stainless steel grades AISI 430, AISI 304 and AISI 316 / 316L.
Grade AISI 430 is a low-carbon chromium-iron stainless steel and contains no nickel at all. Thus, oxidative reactions can occur in a very short time with this steel grade and the application of the material is therefore rather limited.
Material AISI 304 is probably the most common grade in the stainless steel family and contains at least 17.5 % chromium and 8 % nickel. This nickel content ensures the formation of an oxide layer on the surface, which gives the steel good corrosion resistance and makes it resistant to a wide range of chemicals. These properties enable AISI 304 to be used in many areas, such as architecture and the building industry, the food industry, the construction industry, apparatus and mechanical engineering, vehicle construction, sanitary and catering products, household appliances and many more.
AISI 316 / 316L is one of the austenitic steels that is particularly resistant to corrosion thanks to the presence of nickel (at least 10 %) and molybdenum (at least 2 %). This material is therefore recommended for use in environments where there are particularly aggressive factors such as chemical stress, sea water, adverse weather conditions or similar. It is used in the architecture and construction industry for projects near the sea and air with high salt content or other locations that place higher demands on the material in terms of their quality. Grade AISI 316 / 316L is also found in large quantities in the pharmaceutical and medical industries, in tanks, silos and containers, yacht and ship construction only to name a few.
mirrorINOX: Your professionals for (stainless) steel
mirrorINOX offers a selection of high-quality surface treatments in the stainless steel segment. For the most part, we use raw material of the grades AISI 304 and AISI 316.
However, we also mirror polish, grit polish, beadblast, PVD / TiN and nanoINOX® coat the materials AISI 430, AISI 316Ti, AISI 316L and even AISI 318LN (“Duplex”) to protect their surfaces and give them an aesthetic, visual appearance and additional functional properties.
When it comes to value-enhancing and trend-setting treatments for your stainless steel surfaces, mirrorINOX is your No. 1 partner for applications of the highest quality.